What we do
Factory diagnostics
We conduct factory diagnostics using our proprietary Global Benchmarking metrics (*GBM), fine-tuned through over 1,000 diagnostic records. Our clients benefit from exclusive insights derived from GBM assessment, honed through numerous factory diagnostics projects.
We visualize the strengths, weaknesses, issues, and challenges of your factories, and propose Kaizen plans tailored towards your aspirations.
Perfect for…
- Companies seeking an objective assessment of their factories' current Kaizen capabilities.
- Companies aiming to identify gaps between the current state and the aspired state of their factories and to develop Kaizen plans for achieving those aspirations. Companies aspiring to create opportunities for initiating Kaizen efforts.
Why go with our factory diagnostics?
- We quantify the extent of TPS Kaizen using our unique evaluation metrics, GBM.
- Built on a foundation of extensive diagnostic experience from over a thousand projects, our objective evaluations, at a global standard, precisely assess the strengths, weaknesses, and challenges of your factory.
- Based on the diagnostic results from GBM, we will develop and propose Kaizen plans (a mid-to-long-term Kaizen plan spanning 3 to 5 years).
What is Global Benchmarking?
Based on the principles of the Total Toyota Production System (T-TPS), we assess the Kaizen capabilities of factories using global standards. There are six evaluation criteria: 1) Motivating of teams, 2) Shop management, 3) Workers, 4) Production control, 5) Equipment, and 6) Quality.
We rate these six criteria on a five-point scale and determine the factory’s level based on the overall score.
Guided by the benchmark of GBM evaluation results, our goal is to elevate assessment scores through ongoing Kaizen activities. We are dedicated to advancing towards the establishment of a robust factory with a thriving Kaizen culture, ultimately achieving higher levels of quality and productivity in manufacturing.
We rate these six criteria on a five-point scale and determine the factory’s level based on the overall score.
Guided by the benchmark of GBM evaluation results, our goal is to elevate assessment scores through ongoing Kaizen activities. We are dedicated to advancing towards the establishment of a robust factory with a thriving Kaizen culture, ultimately achieving higher levels of quality and productivity in manufacturing.
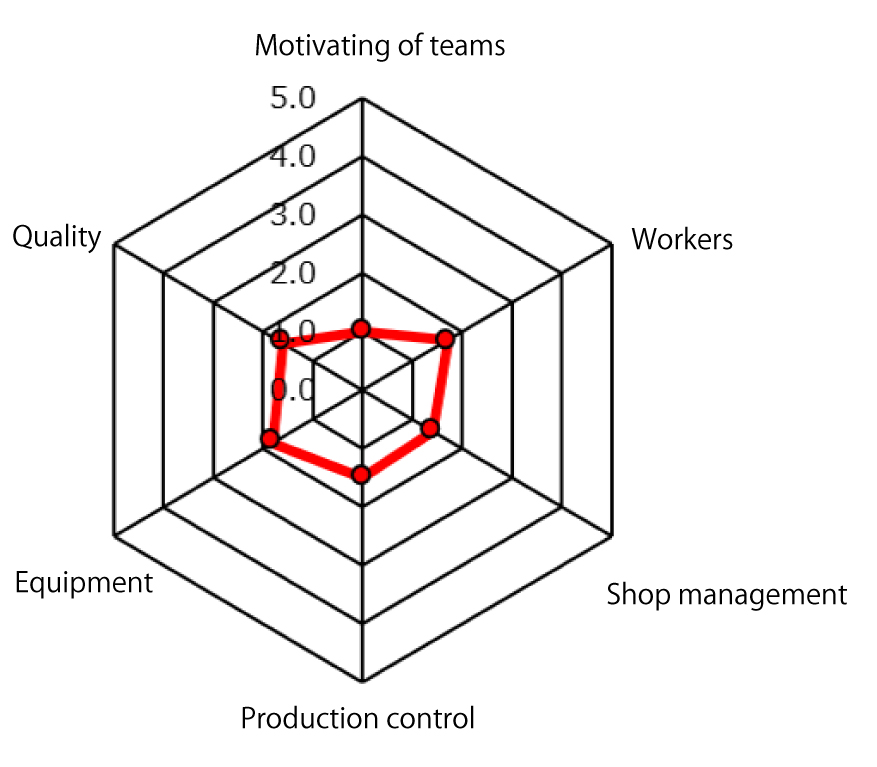

Diagnostic schedule
Scroll sideways▶︎
Stage | Description | |
---|---|---|
Day 1 | (1) Introduction (2–3 hours) |
We conduct on-site visits to gain insights into the operational process. During these visits, we provide a comprehensive explanation of the diagnostic procedure. |
(2) On-site diagnostics (3–4 hours) |
Consultants perform on-site assessments, closely observing factory operations. | |
Day 2 | (3) Aggregation and analysis of diagnostic results (2–3 hours) |
Consultants create diagnostic report documents while, as needed, conducting on-site verbal confirmations at the factory. |
(4) On-site reporting of diagnostic results (1 hour) |
Based on the diagnostic report, consultants will explain the identified issues and Kaizen opportunities (the interim report). | |
Later (Within ten days of completion) |
(5) Submission of documents (diagnostic results and kaizen recommendations) |
We will create a mid-to-long-term Kaizen proposal spanning 3 to 5 years based on the GBM diagnostic results and submit it. ・Factory strengths, weaknesses, current issues, and challenges ・Kaizen opportunities and priorities ・Kaizen approach (a mid-to-long Kaizen plan) |
The results of the GBM assessment serve as benchmarks when confirming Kaizen achievements during the Kaizen process. As the first step towards Kaizen, we strongly encourage you to utilize our factory diagnostics.
Ready to get started? Just curious? Contact us!